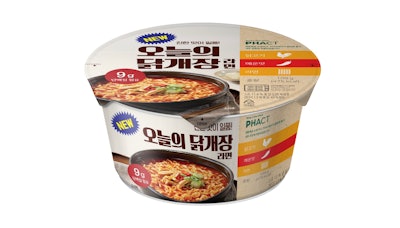
In response to consumer pushback against single-use plastic packaging, brand owners are increasingly finding ways to replace plastic packaging with recyclable paper. The biggest challenge to making the switch, however, has been finding an alternative to the non-recyclable polymer coatings traditionally used with paper packaging to provide a barrier against moisture for food and beverage applications.
One category that has had some recent success in this area is microwavable noodle cups. Last year, Nissin Foods U.S. replaced the nearly five-decades-old polystyrene cup for its Cup Noodle ramen noodle soup line with a proprietary double-wall fiber cup from Graphic Packaging Intl. Following Nissin’s paperization lead, in January, South Korean C-store chain CU, part of BGF Retail, introduced its own microwavable paper cup—in this case compostable—for a new own-brand noodle line, New Today’s Chicken Noodle.
“Korean consumers are very interested in eco-friendly products, which has led Korean manufacturers and distributors to place a strong emphasis on eco-friendly products,” explains Hwang-Bo Min, merchandising department professional, BGF Daily Food Grocery team. “The reason for producing this product was to create Korea’s first eco-friendly Noodle Cup packaging by adding eco-friendly elements to the ramen product that Koreans most enjoy.”
CU’s solution to the plastic coating conundrum was a custom-developed bio-based coating from CJ Biomaterials, a division of South Korea-based CJ CheilJedang and a producer of polyhydroxyalkanoate (PHA) biopolymers. CJ BIO found a way to combine amorphous PHA (aPHA) with polylactic acid (PLA) bioplastic for a microwavable coating that reduces petroleum-based plastic and increases bio-based content without compromising the functionality and quality of the paper cup. The coating also allows the package to be both home- and industrially compostable.
![]() | Read this related article on Nissin Foods’ switch from polystyrene to paper for its microwavable Cup Noodle package. |
PHA and PLA are made from first-generation feedstocks, such as corn and sugarcane. Addressing naysayers’ concerns about using food crops for packaging, CJ Biomaterials Project Leader, Coating Application Part R&D Shim Yoo Kyung notes that these feedstocks provide carbon sequestration, absorbing carbon from the air and accumulating sugar through photosynthesis. “These accumulated sugars are then used to produce biopolymers,” he explains. “Due to the carbon uptake, first-generation feedstocks are also considered renewable resources.”
He adds that according to the European Bioplastics association, first-generation feedstock is currently the most efficient material for the production of bioplastics, as it requires the least amount of land to grow and produces the highest yields. “Also, EUBP says that the surface required to grow sufficient feedstock for today’s bioplastic production accounts for a little more than 0.01% of the global agricultural area, or 5 billion hectares,” he adds.
PHA is one of the newest biopolymers to be produced at scale and is created through microbial metabolic processes. “Many bacteria produce and use PHAs as an energy storage material in nature,” says the company. “CJ Biomaterials’ PHAs are produced through aerobic fermentation, converting natural sugars [from first-generation feedstock] into PHA polymers directly inside microbial bio-factories comprising standard stirred, aerated fermentation tanks. Each fermentation consists of a growth phase, during which empty cells—the ‘bio-factories’—are grown to target concentrations, followed by a production phase, during which the cells fill up with PHA.”
According to the company, PHAs work well as modifiers to other polymers or biopolymers and can increase bio-based content, accelerate biodegradation, and improve the functional properties of resins and finished products. When compared with more widely used semi-crystalline PHA, aPHA (branded PHACT A1000P by CJ BIO) is a softer, more rubbery biopolymer that offers fundamentally different performance characteristics.
![]() | Watch this related video, “Exploring Paper Packaging as a Sustainable Solution: Innovations and Pros & Cons” |
In the case of the coating for CU’s noodle cups, using aPHA with PLA enhanced the processability of PLA by providing flexibility and allowing for more stable use across a wide range of temperatures. “It also exhibits good oil barrier properties, surpassing conventional polypropylene coating while providing a 100% bio-based solution,” says Max Senechal, executive vice president and chief commercial officer at CJ Biomaterials.
Creating the coating for the CU noodle cup was not without its challenges, however. “Finding the optimal processing condition for blending aPHA and PLA was the biggest hurdle due to differences in thermal properties from each other,” explains Yoo Kyung. “It is necessary for the two resins to blend perfectly under the same conditions and repelletize into one resin, but PLA melts at a temperature close to 200°C, while aPHA goes through thermal decomposition even at 150℃, losing its properties. Therefore, CJ Biomaterials developed its own recipe to perfectly blend these two materials, from selecting the suitable PLA grade, securing the composition ratio, including additives, and optimizing the processing conditions in the extruder.
“Next, unlike other applications, the rheology property is a critical factor in the extrusion coating processing. Developing a recipe that maintains the flowability and melt strength to coat a wide square with a uniform thickness was a major challenge. Therefore, we standardized the flowability and melt strength of all formulations in-house to ensure processability and reproducibility for mass production.”
The final package was manufactured in December 2023 and introduced in CU stores Jan. 3, 2024. The cup and lid are printed with the PHACT brand name and copy detailing the composition of the biodegradable coating used inside the cup. “CU wanted to show that this is a product that uses PHACT,” says BGF’s Min. “We wanted to show customers that CU develops a variety of eco-friendly products.
![]() | Read related article, “Biodegradable PHA Water Bottles Make Retail Debut” |
“In Korea, awareness of composting is not high, and the infrastructure is not universally available. Nevertheless, PHA was applied to the inner coating of the Noodle Cup to improve sustainability by using bio-based coating.”
Despite consumers’ inexperience with compostable packaging, Min notes that they are interested in the development of new products. “Although the eco-friendly concept may seem unfamiliar when it comes to Noodle Cup, customers believe that they are contributing to the environment by purchasing those eco-friendly products,” she says. PW