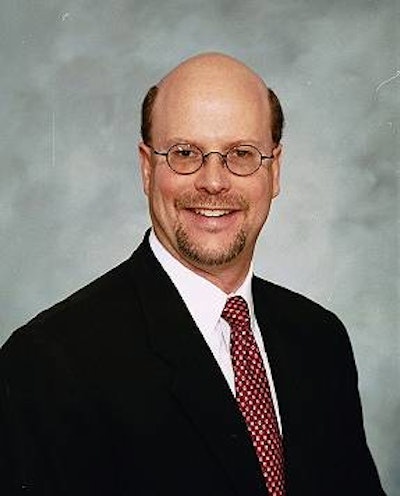
Commissioned by the Fibre Box Association (FBA) RFID Task Group, a new study helps corrugated packaging suppliers understand and plan for the future as vital partners in the supply chain.
The RFID Task Group recognized that studies had already been done examining the impact of RFID on other portions of the supply chain, specifically retailers and consumer goods firms, but no work had been published regarding the impact on packaging suppliers. Therefore, the RFID Task Group commissioned Forrester Consulting to develop a study in July-September 2004. The purpose of the study was to estimate the net effect on a corrugated box manufacturer of supplying RFID-enabled corrugated containers.
With RFID a rapidly emerging trend in the consumer goods and retail industry, it is very likely that RFID tags will soon be requested on finished corrugated boxes, bearing a significant cost impact on a corrugated box plant.
The study indicates that RFID implementation, using what it refers to as today’s high cost/low reliability tags, will add significant cost to corrugated box-making operations. Operational problems such as removing boxes with defective tags and capital improvements required for in-line tag application also were identified. At this time, any operational benefits of RFID implementation for box converters will not offset these extra costs.
Implications for packagers
Brian O’Banion, FBA vice president, spoke with RFID Antenna about the study in an exclusive interview. O’Banion says there’s an underlying sentiment that if consumer packaged goods companies (CPGs) could only move tag application farther back up the supply chain (to box converters), then everything will work for everyone.
“But that is not true, which is why we did the study,” he says.
For the purposes of the study, the assumption was made that the tags are in the form of applied labels rather than embedded tags. That was the current technology when the study was commissioned last summer, O’Banion explains. He points to several reasons that embedding tags are not currently practical, including the fact that typically multiple orders are produced simultaneously on a single web, so tag placement would be very challenging.
“If our members’ customers want those types of services, it can be provided,” says O’Banion. “It’s not a question of unwillingness, but people have to recognize that it’s not as simple to do as it appears on the surface. It may be more cost-effective to initiate RFID at some other point.”
Study parameters
For the study, Forrester Consulting created a costs/benefits model and supporting report for a fictional, yet representative U.S. corrugated box manufacturer. The scope of the study was limited to the converting operation. Focused on make-to-order corrugated boxes, the study defined requirements and costs for in-line tagging on flexo-folder-gluers and specialty folder-gluers, as well as a representative company’s production operations and RFID approach. All operational assumptions were based on plant visits, user interviews and industry data where available.
The model was then used to detail the potential RFID benefits in corrugated box production and distribution, quantify the incremental capital expenses and overall annual costs, and compute net benefit-to-cost on a three-year basis. Costs were then presented by key financial metrics.
The summary report and model are available to FBA member companies, which produce more than 90 percent of all corrugated manufactured in the U.S. CPGs with an interest in obtaining RFID-enabled shipping containers are encouraged to discuss their packaging needs with their corrugated suppliers.