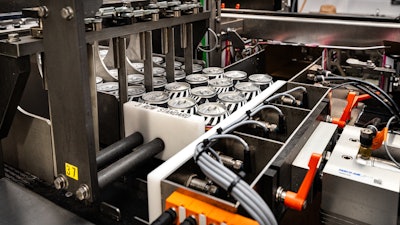
The Shop Beer Co. of Tempe, Ariz., has seen steady growth since its founding in 2016. No surprise, then, that a new canning line went into operation in early 2024.
“We decommissioned a canning line that was anchored by a six-head filler,” says brewery president Dylan DeMiguel. “That equipment is still in great condition and we’re looking to sell it. We just outgrew it.”
In picking equipment for the new line, two packaging machinery suppliers represented in the old line were called on once again: Ska Fabricating and Pneumatic Scale Angelus, a BW Packaging company. Ska specializes in depalletizing, palletizing, and conveying systems, and it’s worth pointing out that The Shop also has two Ska systems at its sister company Handsome Packaging. Located about a mile from the brewery, Handsome Packaging is where full-body shrink sleeves are applied for beverage marketers of all stripes who choose not to buy pre-printed cans but don’t want the hassle of applying their own shrink sleeve labels in house. Cans being filled on The Shop’s new canning line are all decorated at Handsome Packaging.
According to David Arnce, founder and creative director of The Shop, the existence of Handsome Packaging has a lot to do with the minimum order quantities that various can suppliers were requiring a few years back. “When that came about we saw it as an opportunity for us to not only address our own desire for access to cans in quantities we were comfortable with but also to meet the needs of other beverage producers in the region,” says Arnce.
Operating at Handsome Beverage are Ska’s CIB Depalletizer and FAR Bulk Palletizer. In between the two are theThe 12-head rotary filler delivers 100 cans/min.
Getting back to the new canning line at the brewery, depalletizing of cans is done on a CIB Depalletizing system from Ska Fab. An overhead depalletizer, it sweeps cans off one layer at a time onto a platform where line pressure gradually and gently single files them. Then the cans run down a Mini-S-Grip Lowerator Conveyor also supplied by Ska Fab. “That lowerator played a big role in allowing us to shrink our overall footprint,” says DeMiguel.
On their way through the lowerator, cans pass through a Ska ionized air rinser and a Videojet ink-jet date coder that puts a code on the bottom of each can. Next is filling, done on a Pneumatic Scale Angelus 12-head CB100R rotary machine that has a three-station rotary seamer integrated with it. “It's a very efficient counter pressure filler, so our loss is less than 1%, and we run at about 100 cans per minute on the 12-oz size,” says DeMiguel. “It’s just the right system for the growth trajectory we’re on.”
Exiting the filler/seamer on Nercon's Modular Conveyor Express (MCE) conveyors integrated by Ska Fab, cans pass through a Filtec inspection system that kicks out any cans with low fills. Next is an air knife from Republic Manufacturing that dries the cans before they enter an intermittent motion cartoner from Smurfit Westrock. It produces either 4-count cartons of 16-oz cans or 12-count cartons of 12-oz cans. Supplied by Smurfit Westrock, the 18-pt paperboard cartons are printed offset in four to six colors. The Shop Beer Co.'s 16-oz 4-pack multipack carton, Crispy Blonde Lager.
Changeover from one can size to the other takes about 40 minutes, says Arnce, which he finds very appealing. Perhaps more important is that the machine occupies minimal space. “We went for a year hand packing cans into cartons, so putting that cartoner in was one of the easiest decisions we ever made,” says Arnce. “And the training that came along with it was great.”
One task still done by hand is the erection of corrugated trays and the loading of filled cartons into those trays. Arnce says automating this would be plenty attractive, but space constraints have so far ruled that out. All the same, he’s pleased with how things have shaken out now that the new canning line is in operation. “While we need two operators handling the corrugated trays, we need only two on the upstream depalletizing, filling, seaming, and cartoning operations,” he says. “The line has been a welcome addition.” PW