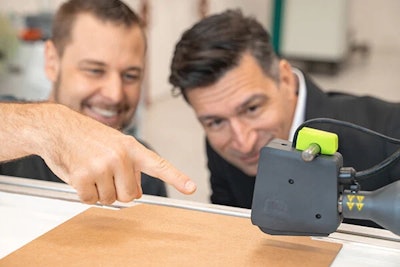
This content was written and submitted by the supplier. It has only been modified to comply with this publication’s space and style.
Robatech's all-electric Volta hot melt jetting head has received an upgrade that makes it even more powerful. With the integrated stitching function, companies can now easily reduce their adhesive consumption by up to 60%—and thus successfully counteract rising production costs.
New: Stitching function integrated in application head
It is now even easier to divide glue beads into shorter beads or glue dots with the Volta application head. The application head control defines how much adhesive is to be saved. This process significantly reduces adhesive consumption without compromising the quality of the application. On the contrary: it even improves adhesion.
Focus on sustainability and energy efficiency
In addition to the savings potential in adhesive, Volta scores with 60% lower energy consumption compared to conventional pneumatic application heads. It operates entirely without compressed air, which reduces maintenance work and cuts costs. The jetting head is also robust and durable—now with a service life of up to 2 billion operating cycles. All of this helps to significantly reduce the carbon footprint of production operations.
“Volta is the answer to the growing challenges of rising production costs,” explains Rolf Gräser, Industry Manager Packaging. “With this solution, we offer our customers not only cost efficiency, but also a sustainable and future-oriented alternative for adhesive application.”
Straightforward integration into existing production lines
The Volta application head can be easily integrated into existing production lines, regardless of the manufacturer of the existing application heads or adhesive application system. Integration takes place via a 24 VDC connection without a booster; an external control is no longer necessary, even for the stitching function.